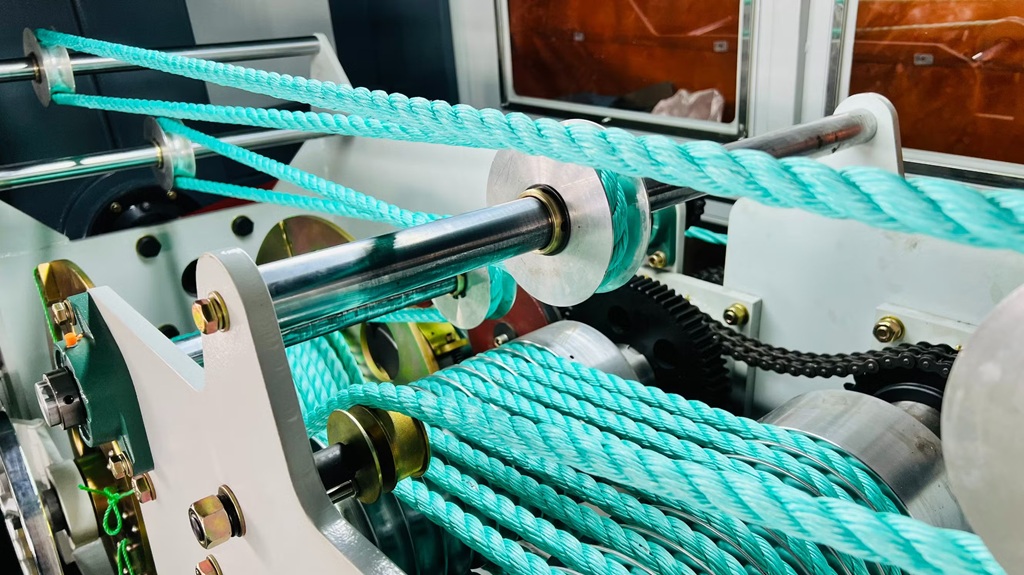
The Unseen Titans: Inside the World of Industrial Rope Making Machines
Rope. It’s a simple concept, yet few tools have shaped human civilization quite like it. From the colossal stones of ancient pyramids hoisted into place, to the rigging of ships that explored new worlds, to the life-saving lines used by climbers and rescue teams today, rope is fundamental. But behind almost every modern rope lies a marvel of engineering: the industrial rope making machine. These sophisticated systems have transformed a laborious handcraft into a high-speed, precision manufacturing process, churning out the vital lines that bind, lift, and secure our world.
Contents at a Glance
ToggleThis article delves into the fascinating realm of these machines, exploring their evolution, how they work, the types available, the innovations driving them forward, their vast applications, and what to consider when selecting one.
From Ancient Twists to Modern Titans: The Rope Making Journey
The desire to bind fibers together for strength is ancient. Archaeological evidence points to simple, twisted cordage dating back tens of thousands of years, likely crafted by hand from plant fibers or animal hides. The ancient Egyptians, around 3100 BC, were among the first to document dedicated rope-making tools, essential for their monumental construction projects. Across the globe, civilizations in China utilized hemp fibers, developing early mechanization concepts during the Han Dynasty.
For centuries, however, the dominant method in Europe was the “ropewalk.” These incredibly long, narrow buildings (or sometimes just outdoor paths) dictated the maximum length of a rope. Teams of workers would walk backward, manually twisting fibers fed from spinning wheels into yarns, then yarns into strands, and finally strands into the finished rope. It was strenuous, slow, and space-intensive work. Leonardo da Vinci famously sketched a conceptual rope-making machine in the 1400s, but it remained an unrealized vision for centuries.
The true shift towards mechanization began during the Industrial Revolution. The burgeoning needs of maritime trade and industry demanded longer, stronger, and more consistent ropes than ropewalks could efficiently supply. Patents for rope-making machines began appearing in the early 1800s, like the one issued to Sellers & Bantle in 1807 in the US. These early machines, often hand-cranked or later steam-powered, replicated the twisting actions of the ropewalk but with greater speed and control. Companies like Haskell-Dawes Machine Company emerged in the late 19th and early 20th centuries, producing robust, durable machines – some of which, remarkably, are still operational today, testament to their engineering prowess. The invention of synthetic fibers like nylon in the 1930s, followed by polyester and polypropylene, further revolutionized the industry, demanding machines capable of handling these new materials and enabling ropes with unprecedented properties.
Decoding the Twist: How Industrial Rope Machines Weave Strength
At its heart, making rope, whether by hand or machine, involves twisting. Fibers are twisted into yarns, yarns into strands, and strands into a final rope. This counter-twisting at each stage locks the components together, distributing stress evenly and creating a structure far stronger than the sum of its individual fibers. Industrial rope making machines automate and refine this process with remarkable speed and precision. While designs vary, the fundamental stages remain similar:
-
Material Feed (Pay-Off):
The process begins with the raw material – spools (bobbins) of yarn or wire – loaded onto a creel or directly onto the machine’s input section. These could be natural fibers like cotton or sisal, or synthetic filaments like polypropylene or high-modulus polyethylene (HMPE).
-
Stranding:
This is the first crucial twisting stage. Multiple yarns are drawn from their bobbins and fed through flyers or rotating elements. As these elements revolve around a central axis, they twist the individual yarns together to form a single, cohesive strand. The number of yarns and the tightness of the twist determine the strand’s characteristics. In machines like tubular or planetary stranders, the yarn bobbins themselves rotate within a cage or tube.
-
Closing (Laying):
Once several strands are formed (typically three or four for standard twisted rope), they proceed to the closing stage. Here, a similar but larger-scale twisting process occurs. The strands are fed into another rotating mechanism (the closer or layer) which twists them together – usually in the opposite direction to the strand twist – around a central core (which might be another strand, a smaller rope, or simply empty space). This counter-twist locks the structure, preventing the rope from unraveling under load. The ‘lay’ refers to the direction of this final twist (commonly ‘S’ for left-hand or ‘Z’ for right-hand lay).
-
Tension Control & Haul-Off:
Throughout the process, maintaining consistent tension on the yarns and strands is critical for producing uniform, high-quality rope. Sophisticated tensioning systems and capstans (large, powered wheels that pull the rope through the machine) ensure smooth operation and prevent irregularities.
-
Winding (Take-Up):
Finally, the finished rope is neatly wound onto large spools or coils by an automated take-up system, ready for storage, cutting, or further processing (like splicing).
Modern machines integrate these steps seamlessly, often controlled by Programmable Logic Controllers (PLCs) that allow operators to precisely set parameters like twist levels, speed, and tension for different rope specifications.
A Machine for Every Strand: Types of Rope Making Equipment
The world of industrial rope making machinery is diverse, with different designs optimized for specific materials, rope constructions, and production volumes. Key categories include:
-
Stranding Machines:
These focus on the first stage – creating the strands.
- Tubular Stranders: Yarn bobbins are housed inside rotating tubes. Good for high speeds and often used for wire stranding.
- Planetary Stranders: Bobbins are mounted on cradles that orbit a central axis while remaining upright (like planets around the sun), minimizing extra twist on individual yarns. Ideal for complex constructions and fiber optics.
- Double Twist Stranders: Wire or yarn passes through the machine twice per revolution, effectively doubling the twist applied, leading to very high output speeds.
-
Closing (Laying) Machines:
These take pre-made strands and twist them into the final rope. They can be horizontal or vertical and range dramatically in size depending on the rope diameter being produced. Many modern “rope making machines” actually combine both stranding and closing functions in a single integrated unit, especially for smaller to medium diameters.
-
Braiding Machines:
While technically producing braided structures (interlocking strands in a woven pattern) rather than twisted ones, braiding machines are often discussed alongside rope makers as they produce flexible cordage used in many similar applications. They use carriers that move bobbins in intricate maypole-like patterns.
-
Coiling & Winding Machines:
Essential auxiliary equipment for managing the finished product, creating neat coils or spools of specific lengths.
-
Specialized Machines:
This includes equipment designed specifically for:
- Plastic Rope/Twine: Often integrated with extrusion lines that produce the synthetic filaments directly before twisting (e.g., PP Danline or fibrillated tape).
- Wire Rope: Built robustly to handle the high tensions and weight of steel wires, often incorporating pre-forming heads and sophisticated lubrication systems.
- Large Diameter Ropes: Massive machines required for producing the thick, heavy ropes used in mooring and offshore applications.
- Natural Fiber Ropes: May have specific adaptations for handling fibers like coir or sisal.
The Heart of Production: Materials Transformed by Machine
The versatility of modern rope making machines allows them to work with a vast array of materials, each offering distinct properties:
-
Natural Fibers:
The traditional choice, valued for biodegradability and specific handling characteristics.
- Cotton: Soft, good handling, but lower strength and susceptible to rot. Used in decorative ropes, sash cords, and some traditional applications.
- Jute & Sisal: Coarser fibers, good knot-holding ability, relatively inexpensive. Common in agriculture, packaging, and rustic decor.
- Hemp: Strong natural fiber, historically significant, seeing a resurgence due to sustainability focus.
- Manila (Abaca): Strong, durable natural fiber resistant to saltwater damage, historically vital for maritime use.
- Coir (Coconut Fiber): Buoyant, resistant to saltwater, often used for mats and some marine applications.
-
Synthetic Fibers:
Dominant in industrial applications due to superior strength, durability, and resistance to environmental factors.
- Polypropylene (PP): Lightweight, floats, resistant to water and chemicals, relatively inexpensive. Widely used in general utility, fishing, agriculture (baling twine), and water sports. Often processed in specialized plastic rope machines.
- Polyester (PET): High strength, low stretch, excellent UV and abrasion resistance, maintains strength when wet. Ideal for rigging, mooring lines, winch lines, and safety applications.
- Nylon (Polyamide – PA): Very strong, excellent shock absorption (due to elasticity), good abrasion resistance. Used in dynamic climbing ropes, anchor lines, towing, and safety harnesses. Absorbs water, losing some strength when wet.
- High-Modulus Polyethylene (HMPE/UHMWPE): Includes brands like Dyneema® and Spectra®. Extremely high strength-to-weight ratio (stronger than steel yet floats), low stretch, excellent abrasion and UV resistance. Used in high-performance sailing lines, lifting slings, winch lines, and protective gear. Requires specialized handling and splicing techniques.
-
Wire (Steel):
Used when exceptional strength and resistance to cutting or extreme heat are required. Galvanized or stainless steel options offer corrosion resistance. Found in cranes, elevators, rigging, mooring, and structural applications. Wire rope machines are heavy-duty and incorporate lubrication systems during manufacturing.
The choice of material dictates machine settings, potential speeds, and the final properties of the rope.
Pushing the Boundaries: Innovations Shaping the Future of Rope Making
The rope making industry isn’t static. Manufacturers are constantly seeking ways to improve efficiency, quality, and the capabilities of both machines and the ropes they produce:
- Advanced Automation & Control: PLC controls are standard, enabling precise adjustments of twist, tension, and speed. Integration with sensor technology allows for real-time monitoring of production parameters and quality control, reducing errors and waste.
- Higher Speeds & Efficiency: Machine designs are continually optimized for faster throughput without compromising quality, crucial for meeting market demand, especially for commodity ropes.
- Precision Tension Control: Sophisticated electronic or mechanical systems ensure every yarn and strand is under the correct tension throughout the process, leading to more consistent and reliable ropes.
- Material Versatility & Handling: Machines are becoming more adaptable, capable of handling a wider range of traditional and advanced fibers, including delicate synthetics or abrasive wires.
- Energy Efficiency: Modern designs incorporate energy-saving motors and optimized mechanics to reduce operational costs and environmental impact.
- Enhanced Durability & Coatings: Post-processing treatments and coatings applied during or after manufacturing (like polyurethane coatings for abrasion resistance or heat-setting for stability) are becoming more sophisticated, extending rope life.
- Sustainability Focus: Growing interest in using recycled synthetic materials or bio-based polymers in rope production, alongside efforts to make the manufacturing process itself more sustainable.
- Smart Rope Potential: Research is exploring the integration of fiber optics or conductive elements within ropes to enable real-time monitoring of load, wear, or potential damage – a significant potential advancement for safety-critical applications.
Related: World’s Strongest Rope: Unveiling the Ultimate Tensile Titans
The Unsung Heroes: Where Industrial Ropes Make a Difference
The output of industrial rope making machines is ubiquitous, supporting countless sectors:
- Maritime & Shipping: Mooring lines, towing hawsers, anchor ropes, fishing nets, rigging lines.
- Construction: Crane hoist ropes, lifting slings, safety lines for working at height, elevator cables, support structures.
- Oil & Gas: Heavy-duty mooring lines for platforms, seismic survey cables, umbilical support, lifting operations.
- Mining: Hoist ropes for cages and skips, draglines, conveyor systems.
- Lifting & Material Handling: Crane ropes, winch lines, slings for industrial lifting in factories and warehouses.
- Arboriculture & Forestry: Climbing lines, rigging ropes for tree removal, winch lines for logging.
- Agriculture: Baling twine, general utility ropes, animal handling.
- Safety & Rescue: Static and dynamic climbing ropes, rescue lines, safety harnesses components.
- Recreation: Climbing ropes, sailing lines, waterski tow ropes, decorative ropes.
- Automotive: Internal components (e.g., window regulators), towing straps.
- Utilities: Pulling lines for installing electrical cables or fiber optics.
Without the reliable, high-strength ropes produced by these machines, many modern industries simply could not function.
Selecting Your Workhorse: Choosing the Right Rope Making Machine
For businesses looking to invest in rope production, selecting the right machine is crucial. Key factors to consider include:
- Rope Specifications: What type of rope (twisted, braided?), diameter range, and construction do you need to produce?
- Material Compatibility: Will you use natural fibers, synthetics, wire, or a mix? Ensure the machine is designed for your chosen materials.
- Production Capacity: How much rope (kg/hour or meters/hour) do you need to produce? Match machine capacity (low, medium, high) to your volume requirements.
- Level of Automation: Manual, semi-automatic, or fully automatic? This impacts labor costs, initial investment, and consistency.
- Budget: Prices vary widely based on capacity, features, automation, and manufacturer. Balance initial cost with long-term operational efficiency and durability.
- Space & Utilities: Consider the machine’s footprint, power requirements, and any necessary auxiliary equipment.
- Manufacturer Reputation & Support: Choose established manufacturers (like Mahesh Twisto Tech, Aawadkrupa Plastomech, Hao Yu, and others often found in hubs like Bhavnagar, India, or internationally) known for quality and reliable after-sales service, technical support, and spare parts availability.
- Quality Standards & Certifications: Does the machine meet relevant industry standards (e.g., CE marking)? This impacts the quality and compliance of the ropes produced.
- Customization: Do you need specific features or adjustments for niche products?
Thoroughly defining your production needs is the first step towards making an informed investment.
Related: Decoding the Workhorse: What is the Most Commonly Used Wire Rope?
People Also Ask (FAQs)
-
Q1: How do industrial rope making machines actually create rope?
- A: In essence, they automate twisting. First, they twist individual yarns together to form strands (stranding). Then, they take multiple strands (usually 3 or 4) and twist those together in the opposite direction to form the final rope (closing or laying). Consistent tension and precise twisting are key.
-
Q2: What are the main materials used in these machines?
- A: A wide variety! They use natural fibers (like cotton, jute, sisal, hemp), synthetic fibers (like polypropylene, polyester, nylon, and high-strength HMPE/Dyneema®), and metal wires (primarily steel). The machine must be suited to the specific material.
-
Q3: What’s the difference between a stranded rope machine and a braiding machine?
- A: A stranded rope machine twists strands together, typically in a helical pattern around a core. A braiding machine interweaves strands in a crisscross, maypole-like pattern, creating a different structure often recognized by its flatter or rounder, woven appearance.
-
Q4: What advancements are we seeing in modern rope making machines?
- A: Key advancements include increased automation (using PLCs and sensors for better control and quality monitoring), higher production speeds, greater precision in twist and tension, improved energy efficiency, and the ability to handle advanced high-performance synthetic materials effectively.
-
Q5: Are there different machines for different rope sizes?
- A: Absolutely. Machines range from small units making twine just a few millimeters thick to massive industrial installations capable of producing very large diameter ropes (e.g., 200mm or more) used for ship mooring or offshore platforms. The machine size, power, and configuration are directly related to the intended rope diameter and material.
Conclusion: The Enduring Twist
From the simplest hand-twisted cordage of our ancestors to the complex, automated titans operating in factories today, the journey of rope making mirrors the progress of human ingenuity. Industrial rope making machines are the powerful, often unseen engines driving this essential industry. They transform humble fibers and wires into the incredibly strong and reliable lines that underpin global trade, construction, energy, safety, and recreation. As technology continues to advance, pushing the boundaries of material science and automation, these machines will undoubtedly evolve further, producing ropes that are stronger, smarter, and more sustainable, ready to meet the ever-increasing demands of the modern world. The simple twist, it seems, still has a powerful future ahead.