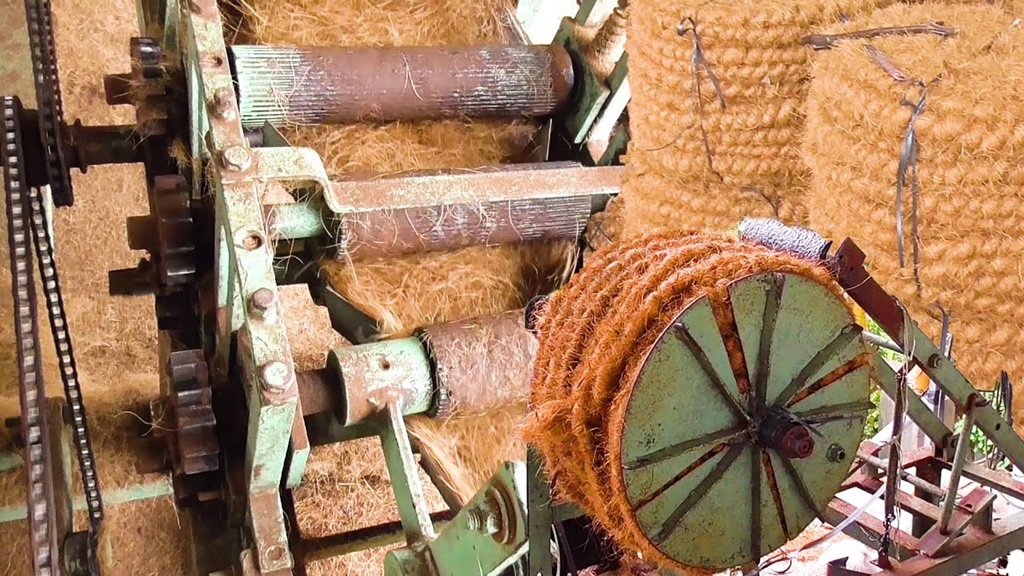
Twisting Tradition into Tomorrow: The Essential Guide to Coconut Coir Rope Making Machines
The humble coconut. It conjures images of tropical beaches and refreshing drinks, but this versatile fruit offers so much more. Hidden within its fibrous husk lies coir – a natural, resilient fiber that humans have ingeniously transformed into rope for centuries. What began as a painstaking manual craft has evolved, thanks to technology. Today, coconut coir rope making machines are revolutionizing this traditional industry, blending age-old utility with modern efficiency and sustainability.
Contents at a Glance
ToggleThis article delves into the world of these fascinating machines, exploring how they work, the different types available, their benefits, the diverse applications of the rope they produce, and the burgeoning market driving their adoption. Whether you’re an entrepreneur in a coconut-rich region like Bangladesh, involved in agriculture, or simply curious about sustainable materials, understanding these machines offers valuable insights.
What Exactly is a Coconut Coir Rope Making Machine?
At its core, a coconut coir rope making machine is a specialized piece of equipment designed to automate or semi-automate the process of twisting coconut coir fibers into strong, usable rope. Think of it as a mechanical evolution of the traditional spinning wheel or ‘ratt’ used for generations.
Its primary function is to take processed coir fibers – extracted from the tough, fibrous husk that sits between the coconut shell and the outer skin – and spin them into yarns, which are then twisted together (plied) to form ropes of varying thicknesses and strengths. These machines streamline what was once an incredibly labor-intensive task, enabling higher production volumes and more consistent product quality. They are the engine driving the modern coir rope industry, transforming a natural byproduct into a valuable commodity.
The Journey: From Coconut Husk to Durable Coir Rope
Creating coir rope, even with machines, is a multi-step process that begins long before the fibers meet the twisting mechanism. It’s a journey from raw agricultural byproduct to a finished, functional product:
-
Harvesting and Dehusking:
It starts with mature coconuts (typically 10-12 months old for stronger, brown coir). The fibrous husk is manually or mechanically separated from the hard inner shell. A skilled manual worker might dehusk around 2,000 coconuts a day, while dehusking machines can significantly increase this rate.
-
Retting:
This crucial step involves soaking the husks in water for an extended period (weeks or even months). Traditionally, this was done in slow-moving rivers or water pits. Microorganisms naturally present in the water break down the pulp (pith) surrounding the fibers, loosening them. While effective, traditional retting can cause water pollution if not managed correctly. Modern methods may involve controlled tanks or mechanical processes to speed this up and mitigate environmental impact. White coir, from less mature coconuts, requires a shorter retting period.
-
Fiber Extraction (Defibering):
Once retted, the husks are beaten or processed through a defibering machine. These machines use rotating drums with steel pins or bars to tear the husk apart, separating the long bristle fibers (used for ropes, brushes, mats) from the shorter mattress fibers and the powdery coir pith (used as a growing medium).
-
Cleaning and Drying:
The separated fibers are washed to remove residual pith, dirt, and debris. They are then thoroughly dried, often in the sun or using mechanical dryers, to reduce moisture content to an optimal level for spinning (typically ensuring humidity is controlled, sometimes specified between 5-40%).
-
Spinning Yarn:
This is where the initial transformation happens. Dried fibers are fed into a spinning machine (which can range from simple hand-cranked devices to automated sections of larger machines). The fibers are drawn out and twisted into single strands of coir yarn.
-
Rope Making:
The coir yarn is then fed into the core rope making machine. Depending on the machine’s design and the desired rope thickness, two, three, or sometimes more strands of yarn are precisely twisted together under tension. This plying process creates the final, strong, and durable coir rope, which is often wound onto a drum or spool for easy handling and storage. Modern machines often integrate the yarn spinning and rope twisting into a continuous, automated process.
Exploring the Types: Finding the Right Fit
Coconut coir rope making machines aren’t one-size-fits-all. They range from basic manual devices to sophisticated automated systems, catering to different scales of operation and investment capacities:
-
Manual ‘Ratt’ Machines:
These are the most traditional form of mechanized assistance, often resembling a large spinning wheel system. They require significant manual labor, typically involving one person turning a crank or wheel while one or two others feed and guide the fibers/yarn.
- Pros: Low initial cost (around ₹15,000 – ₹25,000 / $180 – $300 USD), simple mechanism, suitable for very small-scale or artisanal production.
- Cons: Extremely labor-intensive, slow production speed, quality consistency depends heavily on operator skill, low capacity (perhaps up to 50 kg/day).
-
Semi-Automatic Machines:
These machines incorporate electric motors to power the twisting and winding mechanisms, reducing the physical effort required. Operators still need to feed the fiber or yarn, but the machine handles the core twisting process.
- Pros: Moderate cost (around ₹30,000 – ₹50,000 / $360 – $600 USD), increased production capacity over manual (typically 100-300 kg/day), easier operation, better consistency.
- Cons: Higher initial investment than manual, requires electricity, still needs significant operator involvement.
-
Fully Automatic Machines:
These represent the higher end of coir processing technology. They automate most of the process, from fiber feeding (sometimes integrated with earlier processing steps) to yarn spinning, twisting, and final rope winding. They often feature advanced controls for consistent quality and speed regulation.
- Pros: Highest production capacity (300+ kg/day, some much higher), minimal labor required per unit output, excellent rope quality and consistency, high efficiency.
- Cons: Significant initial investment (₹70,000 – ₹1,20,000+ / $850 – $1500+ USD, potentially much more for large industrial units), require skilled maintenance, need stable power supply.
Portable versions also exist, offering flexibility for on-site production or smaller workshops. The choice depends heavily on the business scale, budget, labor availability, and desired output quality and volume.
Why Embrace Mechanization? The Benefits Unveiled
The shift from manual labor to rope making machines offers compelling advantages for individuals and businesses in the coir industry:
- Dramatically Increased Efficiency: Machines work faster and more consistently than human hands, significantly boosting the volume of rope produced per day. This translates directly to higher potential revenue.
- Improved Rope Quality: Mechanized twisting ensures a uniform diameter, consistent tension, and overall stronger, more reliable rope compared to the variability inherent in hand-spinning.
- Reduced Labor Costs & Strain: Automation drastically cuts down the number of workers needed and alleviates the physically demanding nature of traditional rope making, improving working conditions.
- Scalability: Machines enable businesses to easily scale up production to meet growing market demands, something difficult to achieve with purely manual methods.
- Economic Viability: Faster production and lower labor costs per unit can lead to quicker returns on investment and improved profitability for coir enterprises.
- Sustainability Champion: By efficiently utilizing coconut husks, a widely available agricultural byproduct often considered waste, these machines contribute to a circular economy. They support the production of biodegradable, eco-friendly ropes that serve as alternatives to synthetic options derived from fossil fuels.
Related: The Enduring Versatility of Coconut Coir Rope
Where Does Coir Rope Shine? Diverse Applications
The natural properties of coconut coir rope – strength, durability, abrasion resistance, water resistance (especially saltwater), and biodegradability – make it suitable for a surprisingly wide range of uses:
- Agriculture and Horticulture: A major market. Used for tying plants, supporting vines (especially popular for hops growers as it doesn’t contaminate like metal wire), creating trellises, manufacturing geotextile nets for erosion control on slopes, stabilizing soil, and as moisture-retaining bedding for plants.
- Aquaculture: Its natural resistance to saltwater makes it ideal for oyster and mussel farming (cultch material) and for growing sea squirts without leaching harmful chemicals into the marine environment.
- Construction and Industry: Historically used for scaffolding lashings and binding materials. Today, it finds uses in packaging (as protective padding), and in some niche construction applications focused on natural materials.
- Household Goods and Handicrafts: Coir fibers and ropes are key materials for durable doormats, sturdy brushes, filling for mattresses and upholstery (often rubberized), decorative items, and even linings for reptile terrariums.
- Environmental Applications: Used in bio-engineering for slope stabilization, wetland restoration (coir logs), and creating natural-looking, pest-deterrent fencing in gardens.
Selecting Your Machine: Key Considerations
Choosing the right coconut coir rope making machine requires careful thought beyond just the initial price tag:
- Production Volume: Honestly assess your current and projected output needs (kg per day or shift). Select a machine capacity that aligns with your business goals.
- Budget: Factor in the upfront purchase cost, shipping, installation, potential training, and ongoing operational costs (electricity, maintenance).
- Rope Specifications: What kind of rope do you need to produce? Consider the required diameter, ply count (e.g., 2-ply, 3-ply), and desired tensile strength. Ensure the machine can meet these specs.
- Ease of Use & Maintenance: Look for user-friendly controls and machines known for reliability and relatively simple maintenance procedures. Downtime can be costly.
- Energy Efficiency: Especially for semi-automatic and automatic machines, consider the power consumption (kW or HP rating). Energy-efficient models lower long-term operating costs.
- Space Requirements: Ensure you have adequate floor space for the machine itself, as well as areas for raw material storage and finished product handling. Extraction units often need significant space (e.g., 1 acre).
- Labor Availability: Assess the skill level required to operate and maintain the chosen machine type and the availability of suitable labor in your area.
- Safety Features: Prioritize machines with built-in safety guards, emergency stops, and clear operating procedures to protect workers.
- Manufacturer Support: Consider the reputation of the manufacturer and the availability of spare parts and technical support. Buying from a single reputable source for a whole setup can simplify maintenance.
The Coir Rope Market: Trends and Future Outlook (as of May 2025)
The global market for coconut coir and its products, including rope, is experiencing healthy growth, driven by several key trends:
- The Green Revolution: Increasing consumer and industrial demand for sustainable, biodegradable, and eco-friendly materials is a major tailwind. Coir rope perfectly fits this niche, offering a natural alternative to plastic and synthetic ropes. Its use as a sustainable substitute for peat moss in horticulture is also booming.
- Expanding Agricultural Use: The rise of organic farming, hydroponics, vertical farming, and increased focus on soil health and erosion control are boosting demand for coir-based products like ropes, mats, and grow bags.
- Technological Advancements: Manufacturers are continually innovating, creating more efficient, automated, and energy-saving machines. Integration with other processing steps (like defibering and cleaning) is becoming more common in high-end models.
- Economic Opportunities: The coir industry provides significant employment, particularly in rural areas of coconut-producing nations like India, Sri Lanka, Vietnam, the Philippines, Indonesia, and potentially Bangladesh. Market forecasts predict steady growth, with the overall coco coir market expected to grow significantly in the coming years (e.g., estimates suggest growth from around $650 million USD in 2025 towards $1 billion+ USD by the early 2030s).
- Government Support: Recognizing the economic and environmental potential, governments in some regions (like India’s Coir Board and schemes like Coir Udyami Yojana) are providing support, subsidies, and training to develop the coir sector, encouraging entrepreneurship.
Related: Inside the World of Industrial Rope Making Machines
People Also Ask (FAQs)
How is coir rope made using a machine?
- Coir fibers (from retted and defibered husks) are cleaned, dried, and fed into the machine. It first spins these fibers into yarn. Then, typically 2 or 3 strands of yarn are twisted together under tension by the machine’s mechanism to form the final rope, which is then wound onto a spool.
What are the main types of coir rope machines?
- The main types are Manual (traditional ‘Ratt’, labor-intensive), Semi-Automatic (motor-assisted, moderate output), and Fully Automatic (high output, minimal labor, highest cost).
How much does a coir rope making machine cost?
- Prices vary widely based on type, capacity, and features. Manual machines might start around $180-$300 USD (₹15k-₹25k), semi-automatic around $360-$600+ USD (₹30k-₹50k+), and fully automatic machines can range from $850-$1500+ USD (₹70k-₹1.2L+) to much higher figures for industrial scale setups.
Is coir rope strong and durable?
- Yes, coir rope is known for its natural strength, high abrasion resistance, and durability. It’s also one of the few natural fibers resistant to damage from saltwater.
Is coir rope environmentally friendly?
- Absolutely. It’s made from a renewable resource (coconut husks, often a byproduct), is completely biodegradable, and provides a sustainable alternative to synthetic ropes made from plastics or petrochemicals.
What’s the difference between brown and white coir?
- Brown coir comes from fully mature coconuts; its fibers are thick, strong, and highly abrasion-resistant, ideal for ropes, mats, and brushes. White coir comes from immature green coconuts; its fibers are finer, softer, and weaker, typically used for finer brushes, yarn, and fishing nets (historically).
Can I start a coir rope business?
- Yes, particularly in coconut-growing regions, there is potential. It requires investment in machinery, space for processing, access to a consistent supply of coconut husks, water for retting, reliable power, and establishing market connections to sell the rope. Government schemes might offer support.
Conclusion
The coconut coir rope making machine stands as a powerful symbol of how innovation can enhance traditional industries. It bridges the gap between ancient resourcefulness and modern manufacturing needs. Transforming a humble coconut byproduct into a globally traded commodity with diverse applications. By boosting efficiency, ensuring quality, and reducing arduous labor, these machines unlock significant economic potential. Especially for communities in coconut-producing regions.
More importantly, in an era demanding greater environmental responsibility, the rise of the coir rope machine champions sustainability. It promotes the use of a natural, renewable, and biodegradable resource, offering a practical, eco-friendly alternative to synthetic materials. As the world continues to seek greener solutions, the journey of coir fiber. Twisted into durable rope by increasingly sophisticated machines, is set to become an even more vital thread in the fabric of sustainable industry and agriculture.