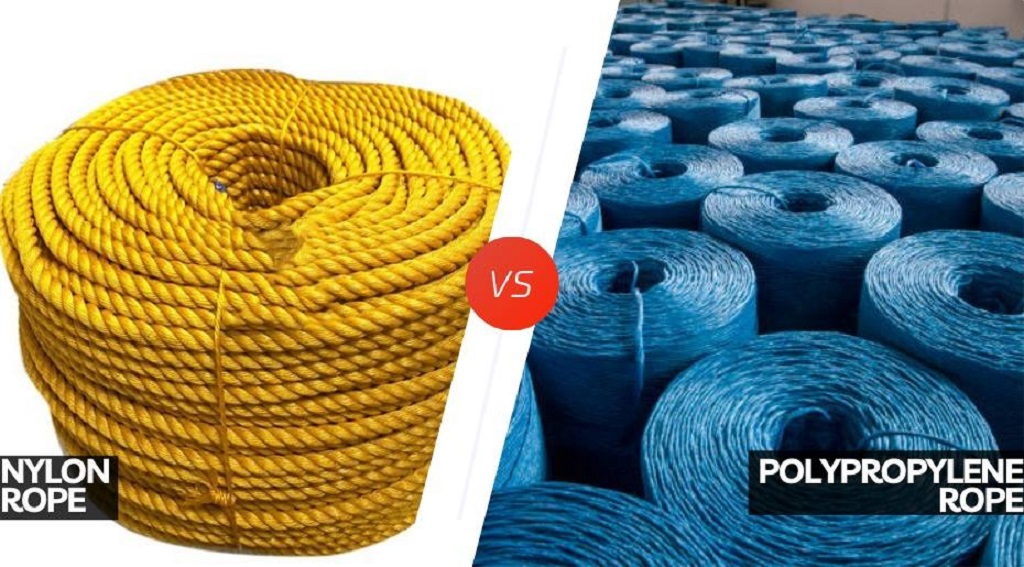
The Complete Guide to Shipping Rope Types: Nylon vs. Polypropylene vs. Manila for Marine Applications
When a cargo ship carrying thousands of containers battles through rough seas, or a fishing vessel secures its nets in stormy weather, the difference between success and disaster often comes down to one critical factor: the rope. Maritime professionals understand that selecting the wrong rope type can lead to equipment failure, cargo loss, or even safety hazards that put lives at risk.
Contents at a Glance
ToggleWhether you’re a seasoned maritime professional, dock worker, or boat owner, understanding the fundamental differences between nylon, polypropylene, and manila rope can save you time, money, and potentially prevent dangerous situations. This comprehensive guide will explore the characteristics, applications, and performance factors of these three essential rope materials used in shipping and marine operations.
Understanding Marine Rope Fundamentals
Before diving into specific rope types, it’s essential to understand what makes a rope suitable for marine applications. Shipping ropes must withstand constant exposure to saltwater, UV radiation, extreme temperatures, and significant mechanical stress. The marine environment is particularly harsh on materials, requiring ropes that maintain their strength and flexibility under challenging conditions.
Marine rope selection depends on several critical factors including load capacity, stretch characteristics, resistance to environmental factors, durability, and cost-effectiveness. Different rope materials excel in different areas, making it crucial to match the rope type to your specific application requirements.
Nylon Rope: The Strength Champion
Nylon rope stands as the premium choice for many heavy-duty marine applications, offering exceptional strength-to-weight ratios and superior shock absorption capabilities. This synthetic material has revolutionized maritime operations since its introduction, providing reliability that natural fiber ropes simply cannot match.
Key Characteristics of Nylon Rope
Nylon rope delivers outstanding tensile strength, often exceeding 6,000 pounds for a 1/2-inch diameter rope. Its most distinctive feature is its ability to stretch up to 25-30% under load, making it ideal for applications requiring shock absorption. This elasticity helps protect both the rope and connected equipment from sudden load changes common in marine environments.
The material exhibits excellent resistance to abrasion, chemicals, and UV degradation when properly treated. Nylon rope maintains its strength across a wide temperature range and resists damage from oils, gasoline, and most marine chemicals. However, it does absorb water, which can reduce its strength by approximately 15% when wet.
Applications in Shipping and Marine Operations
Nylon rope excels in anchor lines, mooring applications, and towing operations where dynamic loads are common. Its shock-absorbing properties make it ideal for docking large vessels, as it can accommodate the constant movement caused by waves and tides without transferring excessive stress to cleats or bollards.
Commercial shipping operations frequently use nylon rope for securing cargo that may experience shifting during transport. The rope’s ability to stretch and recover helps maintain consistent tension on cargo restraints, preventing load shifts that could compromise vessel stability.
Advantages and Limitations
The primary advantages of nylon rope include superior strength, excellent shock absorption, good resistance to environmental factors, and long service life when properly maintained. Its smooth surface resists snagging, making it easier to handle during operations.
However, nylon rope comes with higher upfront costs compared to natural fiber alternatives. Its stretch characteristics, while beneficial for shock absorption, can be problematic in applications requiring minimal elongation. The material also retains memory of previous stretching, which can affect its performance in precision applications.
Polypropylene Rope: The Versatile Performer
Polypropylene rope has gained significant popularity in marine applications due to its unique combination of properties and cost-effectiveness. This synthetic material offers a balanced performance profile that suits many general-purpose marine applications.
Key Characteristics of Polypropylene Rope
Polypropylene rope’s most notable feature is its ability to float, making it invaluable for water rescue operations and applications where rope retrieval from water is necessary. The material exhibits minimal water absorption, maintaining its strength and handling characteristics even when thoroughly soaked.
This rope type offers good chemical resistance and excellent resistance to mildew and rot, common problems with natural fiber ropes in marine environments. Polypropylene rope typically stretches 15-20% under load, providing some shock absorption while maintaining better dimensional stability than nylon.
The material performs well across moderate temperature ranges but can become brittle in extreme cold and may lose strength in high-temperature environments. UV resistance varies significantly depending on the quality of UV stabilizers used during manufacturing.
Applications in Shipping and Marine Operations
Polypropylene rope finds extensive use in water rescue operations, floating safety lines, and applications where rope visibility is important. Its bright colors and floating characteristics make it ideal for marking hazardous areas around vessels or construction sites.
In shipping operations, polypropylene rope serves well for general-purpose securing, temporary rigging, and applications where the rope may come into contact with water. Its resistance to chemicals makes it suitable for use around petroleum products and industrial chemicals commonly found in port facilities.
Advantages and Limitations
Polypropylene rope offers several compelling advantages including its floating capability, resistance to water absorption, good chemical resistance, and relatively low cost. The material handles well in most weather conditions and resists common marine growth that can degrade other rope types.
The limitations include lower strength compared to nylon, reduced UV resistance without proper treatment, and potential degradation in extreme temperatures. The rope can also develop a slippery surface when wet, which may affect handling safety in critical applications.
Manila Rope: The Traditional Choice
Manila rope, made from abaca plant fibers, represents the traditional choice for marine applications. Despite the rise of synthetic alternatives, manila rope continues to find applications where its unique characteristics provide specific advantages.
Key Characteristics of Manila Rope
Manila rope offers excellent grip characteristics, making it easier to handle with bare hands compared to synthetic alternatives. The natural fibers provide good shock absorption through their inherent flexibility, though not to the extent of nylon rope.
The material exhibits good resistance to stretching when dry, typically elongating only 5-10% under load. This dimensional stability makes manila rope suitable for applications requiring precise positioning or minimal give. The rope also provides good resistance to heat, maintaining its integrity at temperatures that might damage synthetic materials.
However, manila rope’s natural fibers are susceptible to rot, mildew, and degradation from prolonged moisture exposure. The material also has lower overall strength compared to synthetic alternatives and requires more frequent inspection and replacement.
Applications in Shipping and Marine Operations
Manila rope remains popular for decorative rigging, traditional boat restoration, and applications where aesthetic appeal is important. Its natural appearance and feel make it ideal for historical vessel restoration and maritime museums.
In functional applications, manila rope serves well for temporary rigging, gymnasium equipment, and situations where its grip characteristics provide safety advantages. Some marine operations prefer manila rope for emergency applications where crew members need to grip the rope quickly without gloves.
Advantages and Limitations
Manila rope’s advantages include superior grip characteristics, good heat resistance, biodegradability, and aesthetic appeal. The material knots well and holds knots securely, making it useful for decorative and functional knot work.
The significant limitations include susceptibility to rot and mildew, lower strength compared to synthetic alternatives, and higher maintenance requirements. The rope also degrades rapidly when stored in damp conditions, making proper storage critical for maintaining its integrity.
Comparative Analysis and Selection Criteria
When selecting rope for specific marine applications, several factors must be considered to ensure optimal performance and safety. Strength requirements, environmental conditions, budget constraints, and specific application needs all play crucial roles in the decision-making process.
Strength and Load Capacity Comparison
Nylon rope typically offers the highest strength-to-weight ratio, making it ideal for heavy-duty applications. A 1/2-inch nylon rope can handle working loads of 1,200-1,500 pounds, compared to 800-1,000 pounds for similar polypropylene rope and 600-800 pounds for manila rope.
For applications requiring maximum strength with minimal weight, nylon rope provides the best performance. However, this advantage comes with higher costs and specific handling requirements that may not be necessary for all applications.
Environmental Resistance Factors
Each rope type responds differently to environmental challenges common in marine settings. Nylon rope offers excellent overall environmental resistance but absorbs water, which can affect its strength and handling characteristics. Polypropylene rope provides superior water resistance but may degrade more quickly under UV exposure without proper treatment.
Manila rope offers good resistance to some environmental factors but is particularly vulnerable to moisture and biological degradation. This makes it unsuitable for permanent outdoor installations but acceptable for temporary or indoor applications.
Cost-Benefit Analysis
Initial cost considerations often favor polypropylene and manila rope over nylon alternatives. However, long-term cost analysis should include factors such as replacement frequency, maintenance requirements, and the potential costs of rope failure.
Nylon rope typically offers the best long-term value for heavy-duty applications despite higher initial costs. Polypropylene rope provides excellent value for general-purpose applications, while manila rope may offer cost advantages for specific short-term or aesthetic applications.
Proper Selection Guidelines
Selecting the appropriate rope type requires careful consideration of specific application requirements, operating conditions, and safety factors. Understanding these selection criteria helps ensure optimal performance and safety in marine operations.
Application-Specific Recommendations
For anchor lines and mooring applications, nylon rope typically provides the best combination of strength, shock absorption, and durability. The material’s ability to stretch and recover helps protect both the rope and connected equipment from dynamic loads.
General-purpose securing and temporary rigging applications often benefit from polypropylene rope’s balanced performance characteristics and cost-effectiveness. The material’s water resistance and chemical compatibility make it suitable for diverse marine environments.
Decorative rigging, traditional restoration projects, and applications requiring superior grip characteristics may benefit from manila rope despite its limitations. The material’s natural appearance and handling characteristics provide advantages in specific situations.
Safety Considerations
Safety should always be the primary consideration when selecting rope for marine applications. Understanding the working load limits, safety factors, and inspection requirements for each rope type helps prevent accidents and equipment failure.
Regular inspection protocols should be established for all rope types, with particular attention to signs of wear, degradation, or damage that could compromise safety. Different rope materials exhibit different failure modes, making material-specific inspection knowledge crucial for maintaining safety standards.
Maintenance and Care Guidelines
Proper maintenance significantly extends rope life and maintains safety standards across all rope types. Understanding material-specific care requirements helps maximize performance and value from your rope investment.
Storage and Handling Best Practices
Proper storage protects rope from environmental damage and maintains its performance characteristics. Nylon and polypropylene ropes should be stored in cool, dry locations away from direct sunlight and chemical exposure. Coiling techniques should minimize kinking and stress concentration points.
Manila rope requires particularly careful storage to prevent moisture accumulation and biological degradation. The material should be thoroughly dried before storage and kept in well-ventilated areas to prevent mildew formation.
Inspection and Replacement Protocols
Regular inspection schedules should be established based on rope type, application, and environmental conditions. Visual inspection should identify signs of wear, cuts, abrasion, or other damage that could compromise rope integrity.
Replacement criteria should be clearly defined and based on manufacturer recommendations, regulatory requirements, and safety considerations. Keeping detailed records of rope installation, inspection, and replacement helps maintain safety standards and optimize replacement schedules.
Read More Also: The Best Ropes for Securing Cargo in Shipping and Logistics
Frequently Asked Questions
Q: How do I determine the right rope diameter for my application?
A: Rope diameter selection depends on your load requirements, available space, and handling considerations. Calculate your working load, apply appropriate safety factors (typically 5:1 to 10:1), and select a rope diameter that provides adequate strength with comfortable handling characteristics.
Q: Can I splice different rope types together?
A: Splicing different rope materials is generally not recommended due to different stretch characteristics, strength properties, and potential compatibility issues. When connections are necessary, use appropriate hardware such as shackles or connectors designed for mixed-material applications.
Q: How often should I replace my marine rope?
A: Replacement frequency depends on rope type, usage intensity, environmental conditions, and inspection results. Establish regular inspection schedules and replace rope when it shows signs of significant wear, reaches manufacturer-recommended service limits, or fails to meet safety requirements.
Q: Which rope type is best for emergency situations?
A: For emergency applications, consider factors such as immediate availability, ease of handling, and reliability under stress. Polypropylene rope often provides good emergency performance due to its floating characteristics and water resistance, while nylon rope offers superior strength for high-load emergency situations.
Q: How do environmental conditions affect rope selection?
A: Environmental factors such as temperature extremes, UV exposure, chemical contact, and moisture levels significantly impact rope performance. Match rope material properties to your specific environmental conditions, and consider protective measures such as UV-resistant treatments or protective coverings when necessary.
Read More Also: Essential Rope Types and Their Practical Uses: A Complete Guide for Every Homeowner
Make the Right Choice for Your Marine Operations
Selecting the appropriate rope type for your shipping and marine applications requires careful consideration of multiple factors including load requirements, environmental conditions, budget constraints, and specific application needs. Nylon rope offers superior strength and shock absorption for heavy-duty applications, polypropylene rope provides excellent versatility and water resistance for general-purpose use, and manila rope delivers traditional handling characteristics for specific applications.
Don’t compromise on safety or performance when it comes to your marine rope selection. Consult with marine supply professionals, review manufacturer specifications, and consider your specific operational requirements to make informed decisions that protect your equipment, cargo, and crew.
Ready to upgrade your marine rope inventory? Contact your local marine supply specialist today to discuss your specific requirements and explore the latest innovations in rope technology. Whether you need heavy-duty nylon rope for commercial shipping operations, versatile polypropylene rope for general marine use, or traditional manila rope for restoration projects, investing in the right rope type will pay dividends in performance, safety, and long-term value.