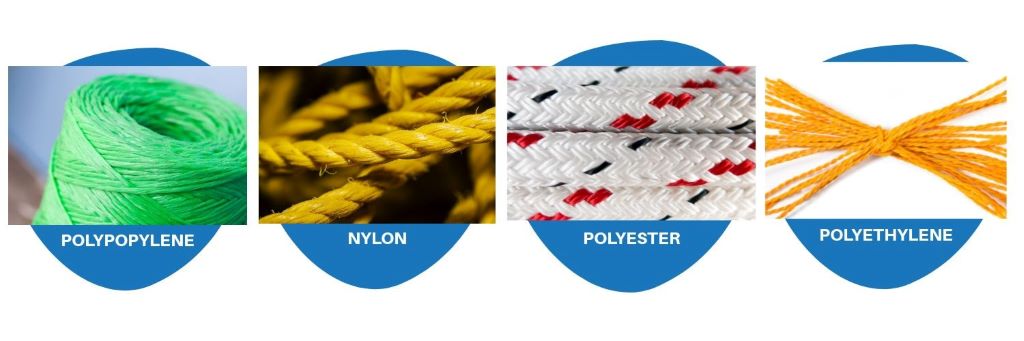
The Three Types of Rope Construction: A Complete Guide to Choosing the Right Rope for Your Needs
Picture this: You’re halfway up a climbing wall when you hear a subtle crack. Your heart races as you realize the rope you trusted with your life might not be as reliable as you thought. The difference between a rope that holds and one that fails often comes down to one crucial factor – how it’s constructed.
Contents at a Glance
ToggleWhether you’re an outdoor enthusiast, marine professional, industrial worker, or simply someone who needs reliable cordage for everyday tasks, understanding rope construction can mean the difference between success and failure, safety and danger. The three fundamental types of rope construction – twisted, braided, and kernmantle – each offer unique advantages that make them suitable for specific applications.
Understanding Rope Construction Fundamentals
Rope construction refers to how individual fibers are assembled and arranged to create the final product. This manufacturing process directly impacts the rope’s strength, flexibility, durability, and performance characteristics. The way fibers are twisted, braided, or arranged determines how the rope will behave under load, how it handles wear and tear, and what applications it’s best suited for.
The choice of construction method isn’t arbitrary – it’s a carefully engineered decision that balances various performance factors. Material selection, intended use, environmental conditions, and safety requirements all influence which construction type manufacturers choose for specific rope applications.
Type 1: Twisted Rope Construction
What is Twisted Rope?
Twisted rope, also known as laid rope, represents the most traditional and widely recognized form of rope construction. This method involves twisting individual fibers into yarns, then twisting these yarns into strands, and finally twisting multiple strands together to form the completed rope. The twisting process creates a helical pattern that’s instantly recognizable and has been used for thousands of years.
How Twisted Rope is Made
The manufacturing process begins with individual fibers – whether natural materials like manila, cotton, or sisal, or synthetic materials like polypropylene or nylon. These fibers are first spun into yarns through a twisting process. Multiple yarns are then twisted together in the opposite direction to form strands, typically three or four strands for most applications. Finally, these strands are twisted together in the original direction to create the finished rope.
This alternating twist direction, known as “reverse lay,” is crucial for rope stability. Without this alternating pattern, the rope would unravel under load. The angle and tightness of the twist significantly impact the rope’s characteristics – tighter twists generally increase strength but reduce flexibility.
Applications and Advantages
Twisted rope construction offers several distinct advantages that make it suitable for many applications. The construction method provides excellent grip characteristics, making it ideal for applications where hand-holding is important. The rope’s surface texture offers natural slip resistance, which is why twisted rope remains popular for gym equipment, playground apparatus, and decorative applications.
Marine environments frequently utilize twisted rope due to its ability to splice easily. When a twisted rope needs repair or when permanent loops are required, the construction allows for traditional splicing techniques that create strong, reliable connections. This makes twisted rope particularly valuable for dock lines, anchor rodes, and rigging applications.
The construction also allows for easy inspection. Wear, damage, or deterioration in twisted rope is typically visible on the surface, making it easier to assess rope condition and determine when replacement is necessary.
Limitations to Consider
Despite its advantages, twisted rope construction has several limitations that users should understand. The twisting process inherently reduces the rope’s strength compared to other construction methods using the same materials. When loaded, twisted rope tends to rotate, which can be problematic in applications where twist must be avoided.
The construction also makes twisted rope more susceptible to abrasion damage. The raised helical pattern creates high spots that contact surfaces first, leading to accelerated wear in applications involving frequent contact with rough surfaces.
Type 2: Braided Rope Construction
Understanding Braided Construction
Braided rope construction involves weaving fibers, yarns, or strands together in an over-and-under pattern, similar to braiding hair but typically more complex. This construction method eliminates the helical twist pattern of traditional rope, creating a more uniform, cylindrical cross-section.
Varieties of Braided Rope
Several braided construction techniques exist, each offering different characteristics. Solid braided rope features a dense, uniform construction throughout, while hollow braided rope creates a tubular structure. Double braided rope, also called braid-on-braid, combines an inner braided core with an outer braided cover, offering enhanced strength and protection.
Single braided rope typically uses 8, 12, or 16 strands woven together, while double braided constructions may use different strand counts for the core and cover to optimize specific performance characteristics.
Performance Characteristics
Braided rope construction offers several performance advantages over twisted rope. The absence of lay direction means braided rope doesn’t rotate under load, making it ideal for applications where twist must be minimized. This characteristic is particularly valuable in pulley systems, winches, and other mechanical applications.
The construction method also provides better strength utilization of the rope’s materials. Without the geometric compromises required by twisting, braided rope can achieve higher working loads relative to its diameter. This makes braided rope popular in applications where strength-to-weight ratio is critical.
Braided rope also handles better in most applications. The smooth, uniform surface reduces friction in pulley systems and makes the rope easier to handle during extended use. The construction distributes loads more evenly across the rope’s cross-section, potentially extending service life.
Common Applications
Marine applications frequently utilize braided rope for running rigging, sheets, and halyards. The rope’s handling characteristics and resistance to rotation make it ideal for applications requiring frequent adjustment or movement through blocks and pulleys.
Industrial lifting and rigging applications also benefit from braided construction. The rope’s strength characteristics and predictable behavior under load make it suitable for crane operations, material handling, and other critical lifting applications.
Recreational applications include water sports, camping, and general outdoor activities where rope performance and handling characteristics are important but extreme conditions aren’t expected.
Type 3: Kernmantle Rope Construction
The Kernmantle System
Kernmantle rope construction, derived from German words meaning “core” and “sheath,” represents the most advanced rope construction technique. This method combines a strong inner core (kern) with a protective outer sheath (mantle), creating a rope that maximizes both strength and durability.
Construction Details
The kernmantle system typically features a parallel-fiber core that carries the majority of the rope’s load. This core may consist of continuous filaments or twisted strands, depending on the specific application requirements. The outer sheath, usually braided, protects the core from abrasion, UV exposure, and other environmental factors while providing the rope’s handling characteristics.
The ratio of core to sheath material varies depending on the rope’s intended use. High-performance applications may use up to 80% core material to maximize strength, while applications requiring enhanced abrasion resistance might use a higher percentage of sheath material.
Performance Advantages
Kernmantle construction offers the highest strength-to-weight ratio of the three construction types. The parallel-fiber core eliminates the strength losses associated with twisting, while the protective sheath maintains this strength over the rope’s service life.
The construction also provides excellent fatigue resistance. The core fibers experience minimal bending stress during use, while the protective sheath absorbs the wear and tear that would otherwise damage the load-bearing elements.
Dynamic performance characteristics can be engineered into kernmantle rope by adjusting core and sheath properties. This allows manufacturers to create ropes with specific elongation characteristics, making them suitable for applications requiring energy absorption or precise handling characteristics.
Critical Applications
Kernmantle rope dominates applications where failure isn’t an option. Rock climbing, mountaineering, and rescue operations rely heavily on kernmantle construction due to its superior strength and reliability characteristics.
Industrial rope access and fall protection systems also utilize kernmantle rope. The construction’s strength and durability make it suitable for applications where human safety depends on rope performance.
Military and tactical applications frequently specify kernmantle rope for its combination of strength, durability, and performance consistency under extreme conditions.
Choosing the Right Construction Type
Application-Specific Considerations
Selecting the appropriate rope construction requires careful consideration of your specific application requirements. For general-purpose applications where cost is a primary concern and performance requirements are modest, twisted rope construction may be sufficient.
Applications requiring frequent handling, good grip characteristics, or traditional splicing techniques often benefit from twisted rope construction. The rope’s texture and splice-ability make it ideal for many traditional rope applications.
When smooth operation through pulleys, resistance to rotation, or improved strength-to-weight ratio is important, braided construction offers significant advantages. The rope’s handling characteristics and performance consistency make it suitable for many modern applications.
For critical applications where maximum strength, durability, or safety is paramount, kernmantle construction provides the best performance. While typically more expensive, the construction’s superior characteristics justify the cost in demanding applications.
Environmental Factors
Environmental conditions significantly influence rope construction selection. UV exposure, chemical exposure, temperature extremes, and abrasion potential all affect rope performance and longevity.
Twisted rope construction may be more susceptible to environmental degradation due to its open structure, while kernmantle construction’s protective sheath offers better environmental resistance.
Safety and Regulatory Considerations
Many industries have specific regulations or standards governing rope construction requirements. Safety-critical applications often mandate specific construction types, testing standards, or certification requirements.
Understanding these requirements is crucial for compliance and safety. Professional applications should always consult relevant industry standards and regulations when selecting rope construction types.
Maintenance and Inspection Guidelines
Construction-Specific Maintenance
Each construction type requires specific maintenance approaches. Twisted rope inspection focuses on surface wear, strand integrity, and overall rope condition. The open construction makes internal inspection difficult, requiring careful attention to surface indicators.
Braided rope inspection involves examining the outer braid for wear, cuts, or other damage. The construction’s uniform surface makes damage detection relatively straightforward.
Kernmantle rope inspection requires attention to both sheath and core condition. Sheath damage may not immediately compromise rope strength, but core damage can be catastrophic. Learning to recognize core damage indicators is crucial for safe kernmantle rope use.
Storage and Handling
Proper storage and handling extend rope life regardless of construction type. Avoiding sharp bends, keeping rope clean and dry, and protecting it from UV exposure and chemicals helps maintain performance characteristics.
Different construction types may have specific storage requirements. Twisted rope should be stored loosely coiled to prevent permanent kinking, while kernmantle rope can typically handle tighter coiling without damage.
Conclusion: Making the Right Choice for Your Needs
Understanding the three types of rope construction – twisted, braided, and kernmantle – empowers you to make informed decisions about rope selection. Each construction type offers unique advantages that make it suitable for specific applications, and choosing the right type can significantly impact your project’s success and safety.
Whether you’re outfitting a boat, setting up a climbing system, or handling industrial lifting operations, the rope construction you choose will directly affect performance, safety, and longevity. Take the time to evaluate your specific needs, environmental conditions, and safety requirements before making your selection.
Ready to upgrade your rope game? Start by assessing your current rope inventory and identifying applications where a different construction type might offer better performance. Research suppliers who specialize in your specific application needs, and don’t hesitate to consult with rope professionals who can provide application-specific guidance. Your next project’s success might depend on making the right rope construction choice today.
Read More:
Ditch the Buckle: Crafting a 550 Paracord Bracelet Without Hardware
From Tropical Shores to Your Garden: The Enduring Versatility of Coconut Coir Rope