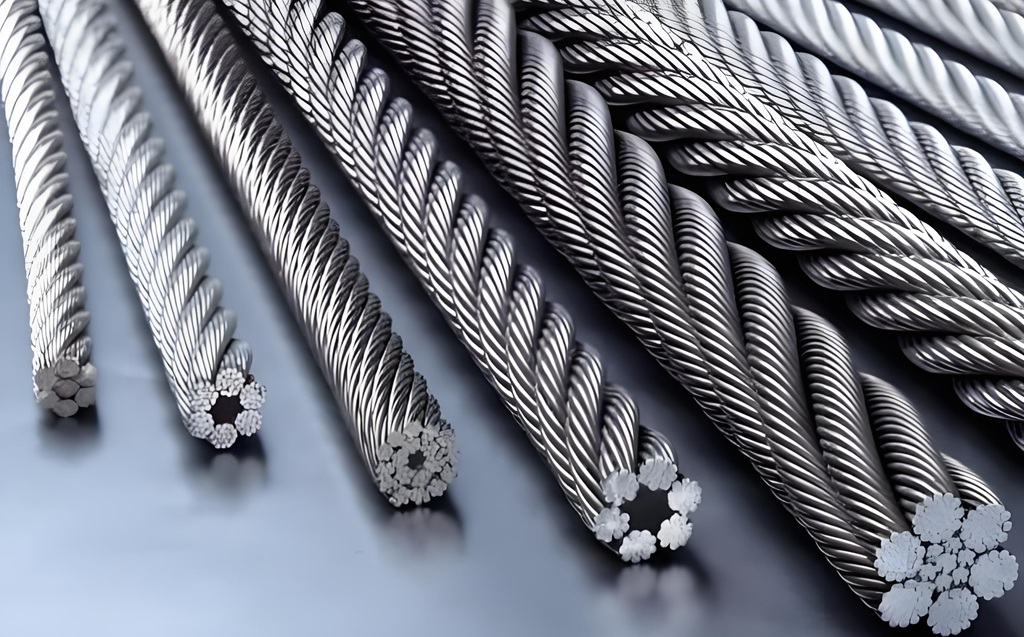
Decoding the Workhorse: What is the Most Commonly Used Wire Rope?
In the intricate dance of modern industry, construction, and transportation, few components are as fundamental yet often overlooked as wire rope. From the towering cranes shaping our city skylines to the elevators whisking us between floors, and the sturdy rigging securing cargo on ships, wire rope is the silent, strong sinew connecting critical operations. Its combination of strength, flexibility, and durability makes it indispensable. But with a vast array of configurations available, a crucial question arises for engineers, riggers, and procurement specialists alike: What wire rope is most commonly used?
Contents at a Glance
ToggleUnderstanding the most prevalent types isn’t just trivia; it sheds light on the ropes that offer the best balance of performance characteristics for the widest range of applications. This article delves into the world of wire rope, identifies the reigning champions of versatility, explores the factors influencing selection, and answers common questions to help you navigate this vital component. As of May 5, 2025, certain classifications continue to dominate general-purpose usage due to their time-tested reliability and adaptability.
Understanding the Basics: What Makes a Wire Rope?
Before pinpointing the most common types, let’s quickly unravel the structure of a typical wire rope. It’s more than just twisted metal; it’s an engineered machine designed to handle tension and movement. The core components are:
- Wires: Individual steel filaments, usually made of high-carbon steel, form the basic building blocks. The diameter and number of wires significantly impact the rope’s properties.
- Strands: Multiple wires are twisted together helically around a central wire or core to form a strand. The pattern of these wires (e.g., Seale, Filler, Warrington) influences the strand’s characteristics.
- Core: The strands are then laid (twisted) around a central core. The core’s primary role is to support the strands, maintain their relative position under load, and provide stability. It can be made of natural or synthetic fibers (Fiber Core – FC) or an independent steel wire rope (Independent Wire Rope Core – IWRC).
- Lay: This refers to the direction the wires are twisted to form strands and the direction the strands are twisted around the core. The most common is Right Regular Lay (RRL), where strands twist right, but wires within the strands twist left, providing stability.
Lubrication is also crucial, applied during manufacturing to reduce internal friction and protect against corrosion.
The Champions of Versatility: Identifying the Most Common Wire Ropes
While specialized applications demand unique constructions (like rotation-resistant ropes for single-line lifts), two classifications consistently emerge as the most frequently used for general-purpose hoisting, lifting, and rigging applications: the 6×19 Class and the 6×36/6×37 Class.
It’s important to note that these classifications are nominal. This means a “6×19” rope doesn’t necessarily have exactly 19 wires per strand, but rather falls within a range (typically 15 to 26 wires per strand). Similarly, the 6×37 class usually encompasses ropes with 27 to 49 wires per strand. The actual construction within the class (like 6×25 Filler Wire or 6×36 Warrington Seale) defines the precise wire arrangement.
## The 6×19 Classification: Strength Meets Durability
Often considered the workhorse of the wire rope world, the 6×19 classification represents a family of ropes built with 6 strands, each typically containing 15 to 26 individual wires. Popular constructions within this class include 6×19 Seale (S), 6×21 Filler Wire (FW), 6×25 Filler Wire (FW), and 6×26 Warrington Seale (WS). Don’t let the “19” fool you; many common ropes in this class, like the 6×25 FW or 6×26 WS, have more than 19 wires per strand but share the core characteristics of the classification.
The defining feature of the 6×19 class is its excellent balance between abrasion resistance and fatigue resistance. The relatively larger outer wires in many 6×19 constructions (like Seale patterns) provide good ruggedness and can withstand external wear and tear, making them suitable for dragging or environments where the rope surface contacts abrasive materials. They also offer good crush resistance, particularly when used with an Independent Wire Rope Core (IWRC), which is important when the rope spools onto a drum, especially in multiple layers. While reasonably flexible, they are generally stiffer than the 6×37 class.
Because of this blend of properties, 6×19 class ropes are incredibly versatile. You’ll find them used extensively in general hoisting applications, crane boom hoists, pendant lines, winch lines, wire rope slings, mooring lines, and some elevator applications. They are a go-to choice when durability and resistance to external damage are primary concerns, coupled with moderate bending requirements. Both Fiber Core (FC) and IWRC options are readily available, allowing users to choose based on flexibility and strength needs.
## The 6×36/6×37 Classification: The Flexible Performer
Think of the 6×36/6×37 classification as the more flexible sibling to the 6×19. These ropes also feature 6 strands, but each strand is composed of a larger number of smaller wires, typically ranging from 27 to 49 wires per strand. The 6×36 Warrington Seale (WS) construction is arguably the most common and widely available within this class today, often superseding older 6×37 designs due to its optimized balance of properties. Other constructions exist, but 6×36 WS serves as a benchmark for the class’s characteristics.
The primary advantage of using more, smaller wires per strand is significantly increased flexibility. This makes 6×36/6×37 class ropes ideal for applications involving frequent bending over sheaves (pulleys) and drums, especially those with relatively small diameters. The increased number of wires also improves fatigue resistance – the rope can withstand more bending cycles before wires start to break. However, this flexibility comes at a trade-off: the smaller individual wires mean the rope generally has lower abrasion resistance compared to the 6×19 class. It’s also slightly less crush resistant, although using an IWRC helps mitigate this.
Given their superior flexibility and fatigue life, 6×36/6×37 class ropes excel as operating ropes on equipment where bending is constant. Common applications include main hoist lines for overhead cranes (EOT cranes), mobile crane hoist ropes, winch lines requiring good spooling on drums, and some larger towing or mooring lines where flexibility aids handling. Like the 6×19 class, they are available with both Fiber Core (FC) for maximum flexibility and Independent Wire Rope Core (IWRC) for enhanced strength and crush resistance.
## Why These Two Rule the Roost
The widespread popularity of the 6×19 and 6×36/6×37 classifications boils down to their inherent versatility and the excellent compromises they strike between competing properties. The 6×19 offers a robust solution prioritizing durability and abrasion resistance, while the 6×36/6×37 provides enhanced flexibility and fatigue life. Together, they cover a vast spectrum of common industrial lifting and pulling needs.
Furthermore, the availability of different core types (IWRC and FC) within these classifications allows users to fine-tune the rope’s performance. Need maximum strength and crush resistance for a demanding hoist? An IWRC version is likely best. Need extra flexibility for a complex reeving system, and crushing isn’t a major concern? A Fiber Core might be suitable (though IWRC is often preferred for longevity and safety margins in critical lifts). This adaptability makes these two classifications the foundation of many wire rope inventories worldwide.
Related: Rope Used for Cutting Down Trees: Essential Gear Guide
Beyond Classification: Critical Factors in Wire Rope Selection
While knowing the most common classifications is helpful, selecting the right wire rope for a specific job requires looking beyond just the 6×19 or 6×36/37 designation. Several other factors are critical:
## Material Matters: Steel, Galvanized, or Stainless?
The base material significantly impacts corrosion resistance and suitability for different environments:
- Bright Steel: This is uncoated high-carbon steel. It’s the standard, most cost-effective option for indoor or dry environments where corrosion isn’t a major concern. It relies on lubrication for protection.
- Galvanized Steel: The steel wires undergo a galvanization process, typically being coated with zinc. This provides good corrosion resistance, making it suitable for outdoor applications, industrial environments, and situations with intermittent exposure to moisture. Drawn Galvanized wire rope retains strength better than standard hot-dip galvanized ropes.
- Stainless Steel: Offering the highest level of corrosion resistance, stainless steel ropes (commonly Grade 304 for general use or Grade 316 for marine/food/chemical environments) are used where rust is unacceptable or where the rope is exposed to saltwater, chemicals, or high humidity. It’s significantly more expensive than bright or galvanized steel.
## The Core Issue: IWRC vs. Fiber Core (FC)
As mentioned, the core type dramatically influences performance:
- IWRC (Independent Wire Rope Core): Essentially a small wire rope itself, the steel core provides firm support to the outer strands, significantly increasing strength (typically by about 7.5%) and resistance to crushing on drums. It also offers better heat resistance compared to fiber cores. It reduces the rope’s elasticity (stretch). IWRC is the preferred choice for most hoisting applications due to its strength and durability.
- FC (Fiber Core): Made from natural fibers (like sisal) or synthetic polymers (like polypropylene), fiber cores offer greater flexibility and elasticity (stretch) than IWRC. They can absorb lubricant well. However, they provide less strength and are much more susceptible to crushing and heat damage (typically limited to operating temperatures below 180°F or 82°C). They are lighter than IWRC ropes.
## Grade Expectations: Understanding Strength (IPS, EIPS, EEIPS)
Wire rope is graded based on its nominal breaking strength. Common grades in North America include:
- IPS (Improved Plow Steel): A baseline standard grade.
- EIPS (Extra Improved Plow Steel): Offers approximately 15% higher breaking strength than IPS. EIPS is a very common and widely specified grade for general-purpose and lifting ropes due to its good balance of strength and cost.
- EEIPS (Extra Extra Improved Plow Steel): Provides roughly 10% more strength than EIPS, used where maximum strength-to-diameter ratio is needed.
Metric standards use grades like 1770 N/mm², 1960 N/mm², and 2160 N/mm², which roughly correspond to IPS, EIPS, and EEIPS respectively, although direct conversion requires checking specific standards (like EN 12385 or ASTM A1023). Always refer to the manufacturer’s specified Minimum Breaking Force (MBF) or Nominal Strength. Remember, the Safe Working Load (SWL) or Working Load Limit (WLL) is typically only a fraction (often 1/5th or 20%) of the nominal breaking strength, determined by a design factor based on the application and safety regulations.
## The Direction of Twist: Understanding Lay (Regular vs. Lang)
The lay describes how wires and strands are twisted:
- Regular Lay: Wires in the strand twist in the opposite direction to the strands around the core. Right Regular Lay (RRL) is the most common. Regular lay ropes are stable, easy to handle, have good crush resistance, and are less prone to kinking and unwinding.
- Lang Lay: Wires in the strand twist in the same direction as the strands around the core (e.g., Right Lang Lay – RLL). This exposes longer lengths of the outer wires, offering better abrasion resistance and flexibility. However, Lang lay ropes are less stable, more prone to untwisting, and require careful handling and installation, often used in specific applications like draglines or excavators where abrasion is severe.
For general hoisting and rigging, Right Regular Lay (RRL) is the overwhelming standard choice.
Related: World’s Strongest Rope: Unveiling the Ultimate Tensile Titans
People Also Ask: Your Wire Rope Questions Answered (FAQs)
-
What is the strongest type of wire rope?
Strength depends on diameter, construction, grade, and core type. For a given diameter, a rope with an IWRC will be stronger than one with an FC. Higher grades (like EEIPS or 2160 N/mm²) are stronger than lower grades (IPS or 1770 N/mm²). Specialized constructions like compacted strand ropes or certain high-performance ropes can offer even higher strength-to-diameter ratios than standard 6-strand ropes. There isn’t one single “strongest” type overall, as it’s relative to size and specific design.
-
What is the main difference between 6×19 and 6×36/6×37 wire rope?
The primary difference lies in the trade-off between abrasion resistance and flexibility/fatigue resistance. 6×19 class ropes generally use fewer, larger wires per strand, making them more resistant to abrasion and crushing but less flexible. 6×36/6×37 class ropes use more, smaller wires per strand, making them more flexible and resistant to bending fatigue, but less resistant to abrasion.
-
What does IWRC mean in wire rope?
IWRC stands for Independent Wire Rope Core. It means the central core of the wire rope is itself a smaller wire rope, typically a 7×7 construction. This provides significant structural support, increases the rope’s overall strength, improves resistance to crushing (especially on drums), and offers better heat resistance compared to a fiber core.
-
How long does wire rope last?
Wire rope lifespan is highly variable and impossible to predict with a fixed timeframe. It depends heavily on factors like: * Operating conditions (load cycles, bending severity, speed) * Environmental exposure (temperature, moisture, chemicals) * Maintenance (lubrication frequency and type) * Installation quality (avoiding kinks, proper drum/sheave grooving) * Inspection frequency and retirement criteria (based on standards like ASME B30 or ISO 4309, looking for broken wires, diameter reduction, corrosion, kinking, etc.). Regular inspection by qualified personnel is key to determining when a rope must be retired from service for safety.
-
What is galvanized wire rope used for?
Galvanized wire rope is used in applications where corrosion resistance is needed due to exposure to moisture, weather, or mildly corrosive industrial environments. Common uses include outdoor construction cranes, winch lines on vehicles or boats, general rigging in exposed conditions, agricultural applications, and some marine uses (though stainless steel is often preferred for harsh saltwater environments).
Conclusion: Choosing the Right Rope for the Job
While the 6×19 and 6×36/6×37 classifications stand out as the most commonly used wire ropes for general purposes thanks to their remarkable versatility, the “best” wire rope is always the one specifically suited to the task at hand. Their popularity stems from offering effective balances – 6×19 favouring durability and abrasion resistance, and 6×36/6×37 prioritizing flexibility and fatigue life.
However, making an informed decision requires drilling down into the specifics. Carefully consider the operating environment (dictating material like bright, galvanized, or stainless steel), the need for strength versus flexibility (influencing core choice between IWRC and FC), the required load capacity (determining the grade like EIPS or EEIPS), and the handling characteristics (usually defaulting to Right Regular Lay).
Always consult manufacturer specifications, adhere to relevant industry standards (like ASTM, EN, ISO, API), and prioritize safety through regular inspection and proper maintenance. Choosing the correct wire rope isn’t just about efficiency; it’s fundamental to ensuring the safety and reliability of critical lifting and pulling operations across countless industries.