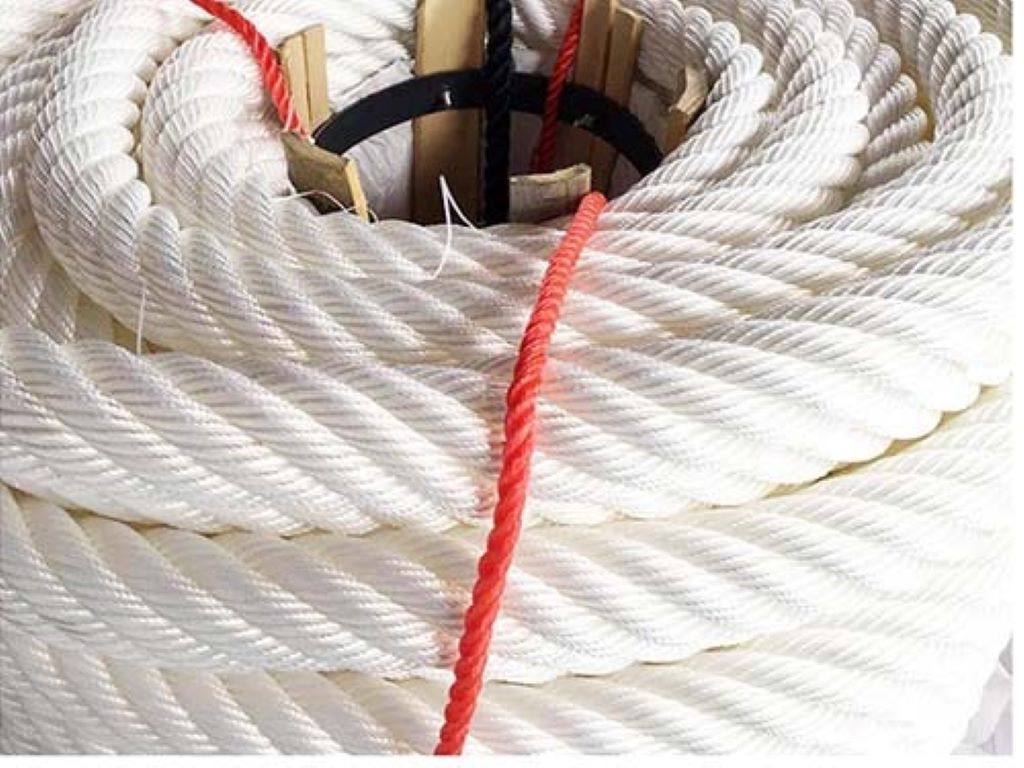
What Type of Rope Do Ships Use? A Complete Guide to Marine Cordage
Picture this: a massive cargo vessel battling 30-foot waves in the North Atlantic, its survival depending entirely on the strength of its mooring lines. Or imagine a luxury yacht gracefully anchored in a Mediterranean harbor, held secure by carefully selected marine rope that must withstand constant saltwater exposure and UV radiation. The difference between safe passage and maritime disaster often comes down to choosing the right type of rope.
Contents at a Glance
ToggleMarine rope selection isn’t just about finding something strong enough to hold a boat – it’s a complex science that maritime professionals have refined over centuries. Modern ships rely on specialized cordage engineered to meet the unique challenges of the marine environment, from extreme weather conditions to chemical exposure and mechanical stress.
The Evolution of Ship Rope: From Natural Fibers to High-Tech Solutions
Traditional sailing vessels once depended entirely on natural fiber ropes made from hemp, manila, cotton, and sisal. These organic materials served maritime purposes for thousands of years, offering decent strength and workability. However, natural fiber ropes had significant limitations: they absorbed water, rotted over time, and lost strength when wet – critical disadvantages in marine applications.
The maritime industry experienced a revolution with the introduction of synthetic rope materials in the mid-20th century. Today’s ships use advanced synthetic fibers that offer superior strength, durability, and resistance to marine conditions. This evolution has dramatically improved maritime safety and operational efficiency.
Primary Types of Marine Rope Used on Modern Ships
Nylon Rope: The Workhorse of Marine Applications
Nylon rope dominates many marine applications due to its exceptional strength-to-weight ratio and elasticity. Ships commonly use nylon rope for:
- Anchor lines: Nylon’s stretch characteristics help absorb shock loads when a vessel rides at anchor
- Dock lines: The material’s elasticity accommodates tidal changes and wave action
- Mooring applications: Commercial harbors rely on nylon’s durability for long-term mooring solutions
The primary advantage of nylon rope lies in its ability to stretch up to 40% under load while maintaining structural integrity. This elasticity proves invaluable during storms or when vessels experience sudden stress loads.
Polyester Rope: Low-Stretch Performance
Polyester rope offers minimal stretch characteristics, making it ideal for applications requiring precise control and stability. Maritime professionals choose polyester for:
- Running rigging: Sail control systems benefit from polyester’s dimensional stability
- Halyards: Flag raising and sail hoisting require minimal stretch for proper operation
- Control lines: Precise boat handling depends on low-stretch rope characteristics
Polyester also demonstrates excellent UV resistance, crucial for rope exposed to constant sunlight in marine environments.
Polypropylene Rope: Buoyant and Chemical Resistant
Polypropylene rope floats on water, making it suitable for specific marine applications where buoyancy is advantageous. Ships use polypropylene for:
- Safety lines: Floating rope helps with water rescue operations
- Temporary applications: Short-term projects benefit from polypropylene’s low cost
- Chemical resistance: Exposure to oils and chemicals makes polypropylene valuable in industrial marine settings
High-Performance Synthetic Fibers
Modern ships increasingly use advanced synthetic materials for demanding applications:
Dyneema/Spectra: These ultra-high molecular weight polyethylene fibers offer strength comparable to steel cable while remaining lightweight and flexible. Large vessels use these materials for critical applications like crane operations and heavy lifting.
Kevlar: Known for its use in bulletproof vests, Kevlar rope provides exceptional strength and heat resistance. Maritime applications include high-stress mooring lines and specialized rigging.
Technora: This aramid fiber offers excellent strength and resistance to chemicals and UV radiation, making it suitable for long-term marine exposure.
Wire Rope: When Synthetic Isn’t Enough
Despite advances in synthetic rope technology, wire rope remains essential for certain marine applications. Ships use wire rope for:
- Winch operations: Heavy lifting requires wire rope’s superior strength and resistance to abrasion
- Crane systems: Construction vessels and cargo ships rely on wire rope for safe lifting operations
- Anchor chains: While technically not rope, wire rope principles apply to anchor chain design and selection
Wire rope offers advantages in applications requiring extreme strength, minimal stretch, and resistance to cutting or abrasion. However, it’s heavier than synthetic alternatives and requires more maintenance.
Specialized Marine Rope Applications
Anchor Rode Systems
Anchor rode systems combine different rope types to optimize performance. A typical setup might include:
- Chain section: Provides weight and abrasion resistance near the anchor
- Nylon rope: Offers stretch and lighter weight for the majority of the rode
- Polyester bridle: Connects the rode to the vessel with minimal stretch
This combination leverages each material’s strengths while minimizing weaknesses.
Towing and Salvage Operations
Marine towing requires specialized rope designed for extreme loads and dynamic conditions. Towing ropes typically feature:
- High breaking strength: Must exceed vessel displacement by significant margins
- Controlled stretch: Enough elasticity to absorb shock loads without excessive elongation
- Abrasion resistance: Protects against damage from contact with vessel surfaces
Emergency and Safety Equipment
Ships carry various rope types for emergency situations:
- Floating safety lines: Polypropylene rope for water rescue operations
- Fire escape ropes: Heat-resistant materials for emergency evacuation
- Rigging repair: Assorted rope types for temporary repairs during emergencies
Factors Affecting Marine Rope Selection
Environmental Conditions
Marine rope selection depends heavily on operating environment:
UV Exposure: Constant sunlight degrades many rope materials. UV-resistant treatments and inherently stable materials like polyester perform better in tropical climates.
Saltwater Corrosion: Synthetic ropes generally resist saltwater better than natural fibers, but specific treatments can enhance performance.
Temperature Extremes: Arctic and tropical operations require rope materials that maintain flexibility and strength across wide temperature ranges.
Load Requirements
Different applications demand specific strength characteristics:
Static loads: Steady, constant forces require rope with appropriate breaking strength and minimal creep.
Dynamic loads: Variable forces demand rope with controlled stretch characteristics to absorb shock loads.
Cyclic loading: Repeated stress cycles require rope engineered for fatigue resistance.
Operational Considerations
Practical factors influence rope selection:
Handling characteristics: Crew safety depends on rope that’s easy to handle and doesn’t create hazards.
Maintenance requirements: Some rope types require more frequent inspection and replacement.
Cost considerations: Initial purchase price must be balanced against service life and performance.
Maintenance and Care of Marine Rope
Proper maintenance extends rope life and ensures safety. Essential maintenance practices include:
Regular inspection: Visual examination for cuts, abrasion, and degradation helps identify potential failures before they occur.
Proper storage: Clean, dry storage away from chemicals and UV exposure preserves rope integrity.
Correct handling: Proper coiling and handling techniques prevent kinks and damage that reduce rope strength.
Replacement scheduling: Proactive replacement based on age, use, and condition prevents unexpected failures.
The Future of Marine Rope Technology
Innovation continues to drive marine rope development. Emerging technologies include:
Smart ropes: Integrated sensors monitor load, wear, and environmental conditions.
Bio-based synthetics: Sustainable materials that maintain performance while reducing environmental impact.
Hybrid constructions: Combining different materials within single rope constructions optimizes performance characteristics.
Nanotechnology: Molecular-level enhancements improve strength, durability, and resistance to environmental factors.
Conclusion
Selecting the right rope for marine applications requires understanding the unique demands of the maritime environment and matching rope characteristics to specific needs. Whether choosing nylon for its elasticity, polyester for its stability, or advanced synthetics for extreme performance, the decision impacts vessel safety, operational efficiency, and crew welfare.
Modern ships rely on carefully selected combinations of rope types, each chosen for its specific properties and applications. As technology continues to advance, marine rope will become even more specialized and capable, further enhancing maritime safety and performance.
Ready to upgrade your vessel’s rope system? Contact marine supply professionals who can assess your specific needs and recommend the optimal rope selection for your applications. Don’t compromise on safety – invest in quality marine rope that will keep your vessel secure and operational when conditions get challenging. Whether you’re outfitting a pleasure craft or managing a commercial fleet, the right rope choice makes all the difference between smooth sailing and maritime mishaps.
Read More:
Child-Safe Rope Climbing Frame Construction: Building Fun and Secure Play Spaces